LPG tanker(VLGC)
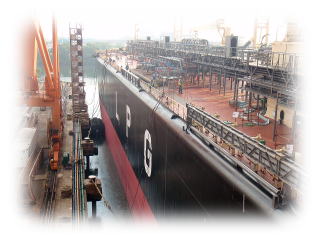
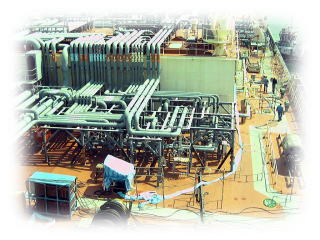
We have proven our reliable technology as a total engineering company by providing a wide range of maintenance services at the dock of an LPG carrier (VLGC). We have earned a high evaluation from the client by conducting preliminary diagnosis by visiting and boarding the ship before dock work, preparing for the work and dock work, and inspecting the dock after completion of dock work by witnessing the first loading and unloading.
A)Preliminary diagnosis by visiting and boarding ship prior to dock work
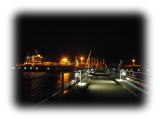
Prior to the dock work, a preliminary diagnosis was conducted to discuss the work, diagnose the current condition of the equipment, and confirm the necessary parts. After confirming the above through preliminary diagnosis, an in-house meeting was held to carefully discuss necessary parts arrangement, information sharing with each maker, and time schedule, etc., to improve work efficiency.
B)Dock work
1)Accuracy inspection of measuring instruments (pressure gauges, thermometers,
level gauges)
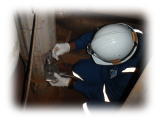
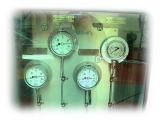
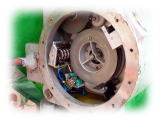
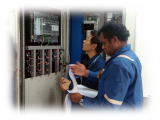
Cargo tanks have extremely large cargo capacities compared to small LPG
carriers, and any malfunction in the cargo tanks can cause errors in the
amount of cargo unloaded. It is extremely important to check the accuracy
of the weighing instruments in order to confirm the accurate amount of
cargo transported.
For LPG / VCM vessels that import and export in Japan, the measuring instruments
and tank tables need to be approved by the customs office and need to be
updated regularly. As with small LPG carriers, the entire process from
explanation and application to the customs office, inspection, and arrangement
of a third-party inspection body is completed, and not only the ship management
company, but also the customs office, shipowner, and third-party inspection
organization. Also received high praise.
2)Disassembly and assembly work and parts supply for cargo pumps and booster pumps
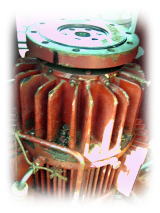
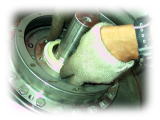
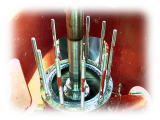
We have replaced all the mechanical seals and ball bearings of the deep well type cargo pumps of European manufacturers. Before the dock, we diagnosed the current state of cargo pump operation, and performed the judgment, arrangement, and replacement work of replacement parts at the dock. Some cargo pumps use special carbon, etc., and it takes a considerable amount of time for delivery. Therefore, we scould take corrective measures in advance by supplying parts in a timely manner based on our prior diagnosis. I did.
3)Cargo compressor disassembly and assembly work and parts supply
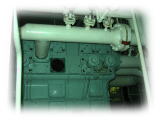
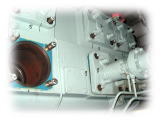
- Prior to the dock, we diagnosed the current status of the cargo compressor operating condition, and determined, arranged for, and replaced all replacement parts at the dock. The compressor intake and discharge valves require maintenance after a certain amount of time of operation. Spare parts of the vessel were used in an efficient rotation, and parts removed during the dock period were serviced and delivered again as spares for the vessel. We submitted the results of the diagnostics and the report at the time of docking, as well as a technical explanation to the ship's classification authority, and obtained their approval.
4)Gas detector (fixed and portable) operation check and parts supply
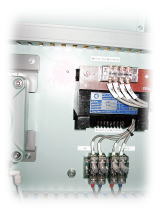
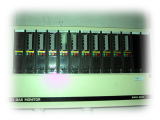
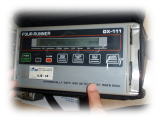
Fixed gas detectors made by an overseas maker had been frequently malfunctioning since the vessel was put into service. At the request of the shipowner, we designed and modified the equipment to work properly with both Western and Japanese equipment, and confirmed that it was working properly. We also verified the operation of the portable multi-gas detector and replaced parts, submitted the report, and provided a technical explanation to the shipowner for approval.
5)Fire detection system operation check and parts supply
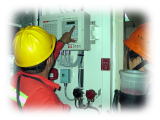
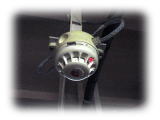
The operation of the fire detection system was checked and parts were replaced, and a report was submitted and a technical explanation was given to the shipowner for approval. Since this vessel has many detectors, we recommend periodic self-inspections to our customers and crew members. Since the vessel crew had already conducted a self-inspection at the dock, MEC's technical explanation and the data display of the vessel data were highly evaluated by the ship's classification authority.
6)Carbon dioxide fire extinguishing system inspection
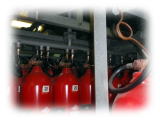
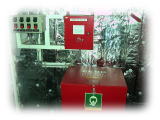
We conducted bottle calibration and operation check of the carbon dioxide fire extinguishing system, submitted the results, and provided technical explanations to the ship's classification authority, which approved the system.
7)Cargo monitoring panel alarm system modification and operation check
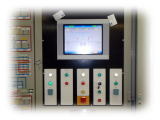
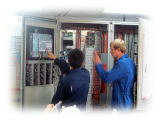
We worked with the software maker and a European engineering company to complete the modification work and check the operation of the system, and submitted a report and technical explanation to the ship classification office for approval. Due to major requirements, inspections of cargo monitoring panels are of particular importance.
8)Hold space inspection
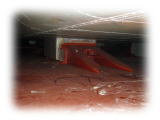
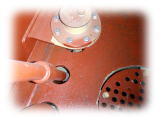
We inspected the tank support system in the hold space, which is the most important part of cargo tank maintenance and inspection, as well as the surrounding structural members, heat insulating materials, etc. We also inspected the building alarm in the hold space to maintain the environment in the hold.
9)Oil mist detector inspection and maintenance
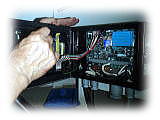
We checked the operation of the oil mist detector of the hydraulic system for controlling the ballast tank in the engine room and performed maintenance. Since the ballast tank control hydraulic system operates at very high pressure of over 100 bar g, it is very dangerous if an oil leak occurs.
10)Inspection and maintenance of oxygen monitor for IGG
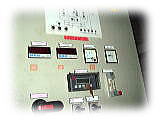
The accuracy of the purity of the IGG (Inert Gas Generator System) is critical with respect to environmental control. For this reason, normal operation of the IGG system is always required. During this dock construction, we confirmed the operation and maintenance of the oxygen monitor for IGG, and received a high level of trust from the client.
11)Engine control valve inspection and maintenance
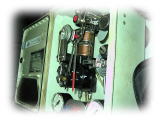
Inspection, maintenance, and adjustment of cooling water and lubricating oil used for cooling the main engine and temperature control valves used for fuel oil heating were performed, and technical explanations were given to the crew members.
12)Compressor room control valve inspection and maintenance
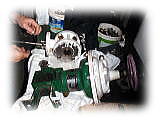
The control valves used in the re-liquefaction system were disassembled
and serviced in the compressor room, parts were replaced, and the control
valves were fine-tuned. As a result, we confirmed that the system functions
properly.
13)Vibration measures
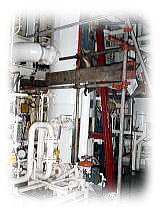
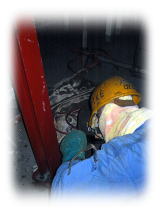
By analyzing the vibration during operation, we worked with the dock to add anti-vibration support to protect each piece of equipment.
14)Tank internal inspection
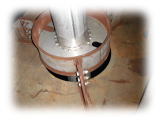

When a tank is opened, an internal inspection of the tank is performed.
We inspected the inside of each tank with the shipowner to ensure that
there were no foreign objects in the tanks or abnormalities in the internal
structure.